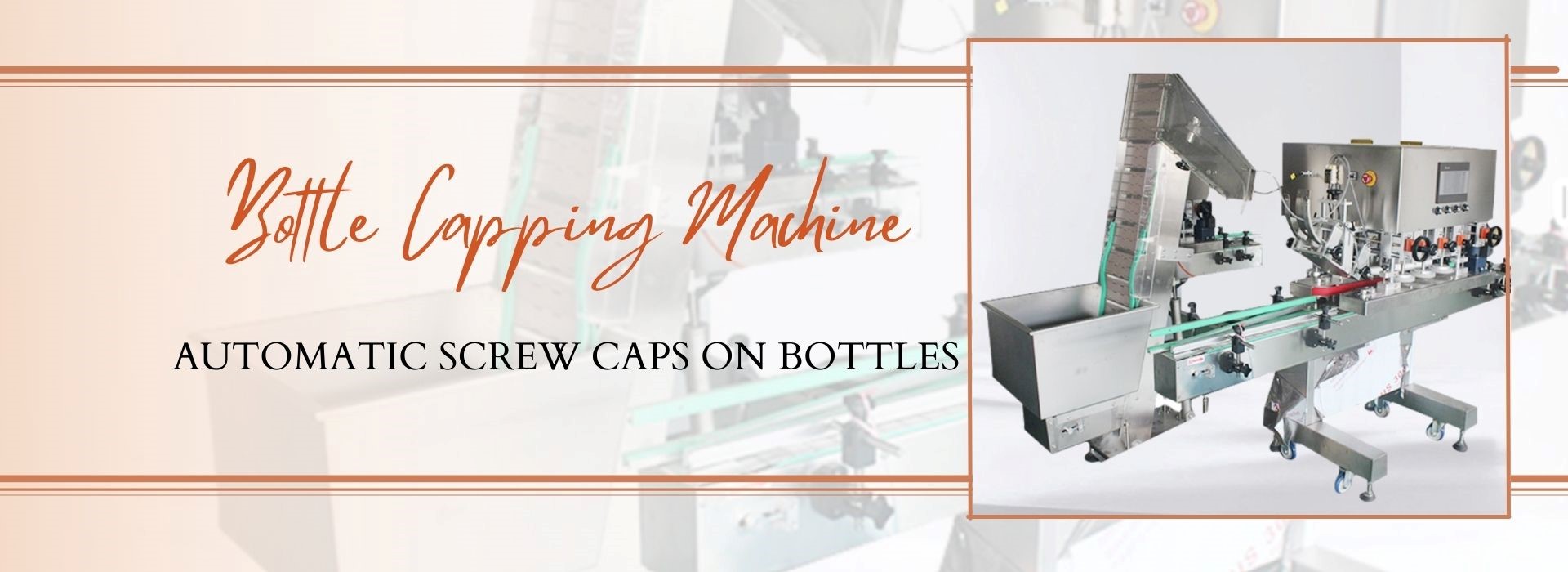
“Intelligent Capping Machine Automation” entails to integrates advanced technologies and systems to streamline the capping process, improve efficiency, and improved overall performance. Here are some of the most important aspects of intelligent automation for a capping machine:
Intelligent automation allows the automatic feeding of caps into the capping machine. Cap elevators, vibratory bowl feeders, and robotic pick-and-place systems can be used to accomplish this. Automating the cap feeding process can reduces the need for manual labor while increasing the speed and accuracy in cap placement.
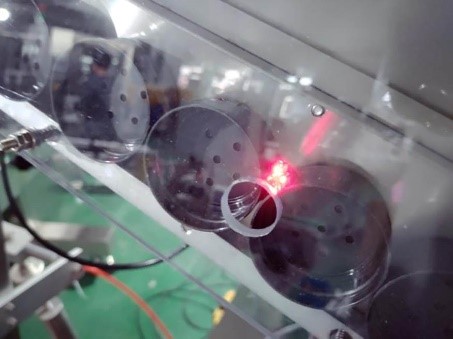
Sensor-based Cap Detection:
Intelligent capping machines detects the presence, position, and orientation of caps on containers using sensors and vision systems. This ensures precise cap alignment and placement, lowering the risk of misalignment or incorrect capping.
Capping Mechanisms that Adapt:
Advanced automation technologies enable the capping machine to adapt on a different cap sizes, shapes, and materials. The machine can automatically adjust its settings to accommodate different caps by incorporating adjustable capping mechanisms, eliminating the need for manual adjustments and reducing downtime during changeovers.

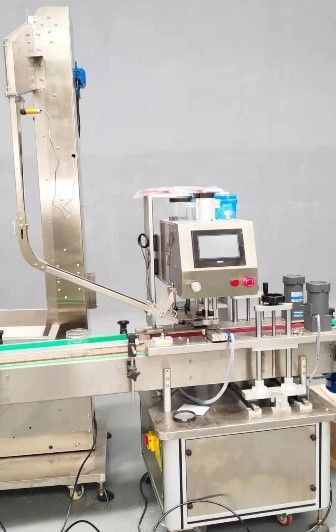
Torque Control and Monitoring:
During the capping process, intelligent automation systems allows’ the precise torque control. Torque sensors in motorized capping heads allows the consistent and accurate torque application to ensure proper sealing while avoiding cap overtightening or under tightening. Real-time torque monitoring detects any abnormalities or deviations immediately, ensuring product quality and preventing problems such as leaks.
Line Control System Integration:
Intelligent capping machines can be seamlessly integrated into overall production line control systems. This integration allows to synchronized operations, data exchange, and coordination with other pieces of equipment such as filling machines, labeling machines, and conveyors. It allows more efficient production process, fewer bottlenecks, and real-time monitoring and control of the capping operation.
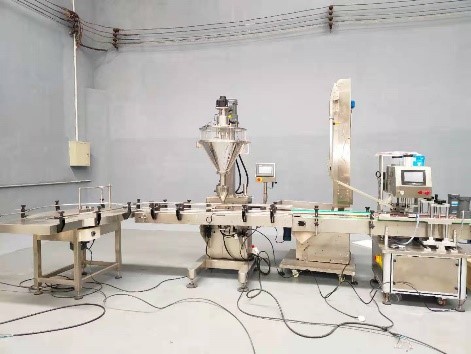
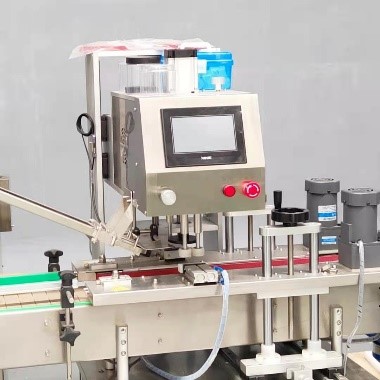
Data Monitoring and Analytics:
Intelligent capping machine automation systems can collect and analyze capping operation data. Torque levels, cap placement accuracy, production rates, and equipment performance are all included. This data can be analyzed to provide valuable insights for optimizing the capping process, identifying potential issues, and improving overall efficiency and quality.
Remote Monitoring and Maintenance:
Some intelligent capping machines have remote monitoring capabilities, which allow operators or technicians to remotely monitor machine performance, diagnose problems, and perform maintenance or troubleshooting. This decreases downtime, improves response times, and increases overall equipment maintenance and uptime.
Manufacturers can benefit from increased productivity, improves quality control, reduced labor requirements, and improved operational efficiency by incorporating intelligent automation into capping machines. It allows for a more efficient and dependable capping process, which contributes to the overall success of production operations.
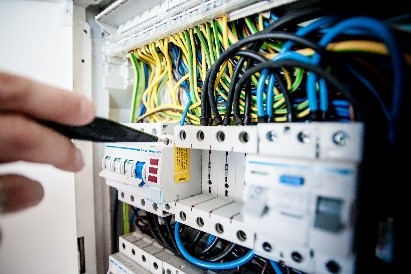
Post time: May-24-2023